About Us
Sheet Metal Fabrication Equipment
-
AHM Automated Storage and Retrieval System
The AHM automated storage and retrieval system features 15 levels of storage space, accommodating various sheet metal sizes for convenient access.
-
Sheet Metal Cutting
Advantages of Automatic Feeding Laser Cutting:
Improved production efficiency
Enhanced cutting precision
Reduction in labor costs
Lower error rates
Increased product consistency
Savings in material costs
Introducing automated laser cutting equipment has further enhanced our processing quality and efficiency. -
Sheet Metal Movement to Punching Machine Effort-Saving DeviceUsing mechanical suction to transport iron plates reduces the risk of accidents caused by the heavy weight of sheet metal during movement.
Sheet Metal Fabrication Equipment
-
German TruPunch 1000 Punching Machine
The TruPunch 1000 punching machine enhances sheet metal manufacturing productivity by automating punching operations, thereby saving labor. Utilizing high-precision German machinery improves product quality, while intelligent nesting optimization significantly reduces material waste, leading to cost savings. -
CNC High-Precision Hydraulic Press Brake
Utilizing a CNC control system, the hydraulic press brake achieves high precision bending and accurate angle control to meet various product fabrication requirements.
-
Six-Axis Automa
Introducing this equipment enables high-precision and multi-angle welding, facilitating partial automation in production. This reduces repetitive tasks, lowers labor costs, and enhances production efficiency.
Complete Line Paint Baking Equipment
-
Powder Coating Machine
We use a French electrostatic powder coating machine, which completes the enclosure painting process from sandblasting to powder coating in one go. -
Sandblasting Rust Removal Chamber
Sandblasting rust removal is a crucial step in the sheet metal fabrication process, aimed at removing rust and other contaminants from metal surfaces to ensure that the produced parts or products meet high-quality and durability standards. -
Powder Coating and Baking Oven
Powder coating is primarily used on metals and other substrates. The process is described as follows:
-
Substrate Preparation: Ensuring the substrate surface is smooth and clean, removing contaminants such as grease, dust, etc.
-
Powder Application: Using an electrostatic powder coating machine to evenly apply the powder coating onto the substrate. The powder particles carry an electrostatic charge, allowing them to automatically adhere to the substrate surface.
-
Curing: After powder application, the coated substrate enters a baking oven or furnace. High temperatures melt the powder, causing it to fuse with the substrate surface and form a cured coating.
-
Cooling and Inspection: Once the coating is cured, the substrate cools down. It undergoes inspections for appearance, thickness, adhesion, etc., to ensure quality standards are met.
-
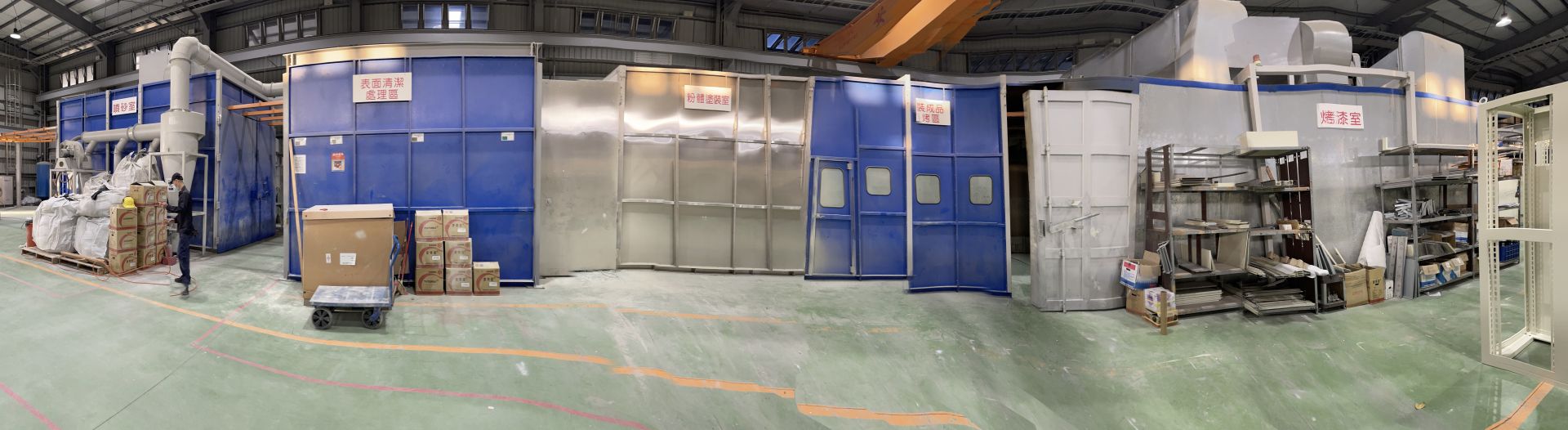