Taichung Factory:04-23581140
Chiayi Factory:05-2955695
HOME
About us
About Us
Electrical Assembly Equipment and Inspection Process
Introduction to the Electrical Assembly Manufacturing Process
-
Material Warehousing and Incoming Inspection
Warehousing: The warehouse management team prepares materials based on project requirements and stores them in the warehouse area. Once materials are prepared, they await issuance to manufacturing personnel.
Quality Assurance Incoming Inspection: After materials arrive, the quality inspection unit conducts inspections based on material inspection standards. Inspection steps include sampling according to the sampling plan, visual inspection, functional testing, and completion of inspection records in the incoming inspection report. -
Production Material Issue
Material Issuance: During manufacturing, materials are issued for each project according to specific requirements. Each item on the material requisition form is checked against specifications, models, etc., to ensure accuracy before issuing the materials. -
Equipment Installation
Equipment Installation: Manufacturing personnel verify the materials list against the equipment assembly drawing before proceeding with installation. Once verified, they refer to the cabinet drawing to accurately position and install equipment components according to the specified locations.
Introduction to the Electrical Assembly Manufacturing Process
-
Control and Power Wiring
Control Wiring: Manufacturing personnel select the appropriate wiring size and terminals according to the specifications on the drawings. They proceed to fabricate the wiring by connecting equipment to equipment based on the marked points on the equipment drawings, ensuring the functionality of the equipment is achieved.
-
Copper Bar Processing and Assembly
Copper Bar Installation and Fabrication: Based on the drawings or current load requirements, select the appropriate size of copper bars for fabrication. After cutting, bending, punching, and other processes, the copper bars are produced. The copper bars are then coated with insulation according to the corresponding phase. After processing, the copper bars are installed inside the panel body and used to connect electrical components using screws. -
Introduction to Quality Inspection Process
-
Box Inspection
Box inspection involves verifying dimensions, material, thickness, and ensuring compliance with design specifications according to the drawing.
Material, Drawing, Equipment Assembly, Wiring, and Busbar FabricationVerification. -
Material Verification: The materials used in the distribution panel installation must match the materials checklist.
Drawing Verification: The completed assembly materials loop must correspond with the single-line diagram, specifications, and quantities.
Equipment Assembly Verification: Ensure that equipment distances are sufficient and installations are correct.
Wiring Verification: Confirm that wiring types, colors, and sizes comply with manufacturing standards and ensure the wiring is aesthetically pleasing.
Busbar Fabrication Verification: Verify that the selected size of the busbars matches the specifications on the drawing. -
Main Circuit Resistance Testing
Main circuit resistance testing involves measuring the contact points of switchgear equipment to check for any poor conductor contact conditions.
Introduction to the Quality Inspection Process
-
Mechanism Operation Testing
Mechanism operation testing involves verifying if the mechanical equipment can function properly. This includes checking if interlocking devices such as ATS (Automatic Transfer Switch), DS (Disconnect Switch), CB (Circuit Breaker), and LBS (Load Break Switch) can be properly engaged, contacted, and released. -
Insulation Resistance Test
The insulation resistance test involves measuring whether the insulation resistance at various points meets the specified standard values. -
Functional Testing
The functional testing involves confirming whether the panel operates correctly and whether the instrument functions according to the requirements specified in the drawings. It verifies whether all functionalities and displays are operating normally as per the design specifications.
Introduction to the Quality Inspection Process
-
Dielectric Strength Test
The dielectric strength test involves applying commercial frequency AC voltage (measured by a voltmeter) to the device grounded for one minute without any abnormal occurrences. -
Screw Inspection
For the screws used to secure the copper bars in equipment, test the torque according to the torque specification table marked on the screws. -
TAF Laboratory Testing Equipment
-
comprehensive testing platform" or "integrated testing station
-
AC withstand voltage test equipment (60kV)
-
low resistance meter
TAF Laboratory Testing Equipment
-
film thickness gauge
-
vernier caliper
-
high resistance meter
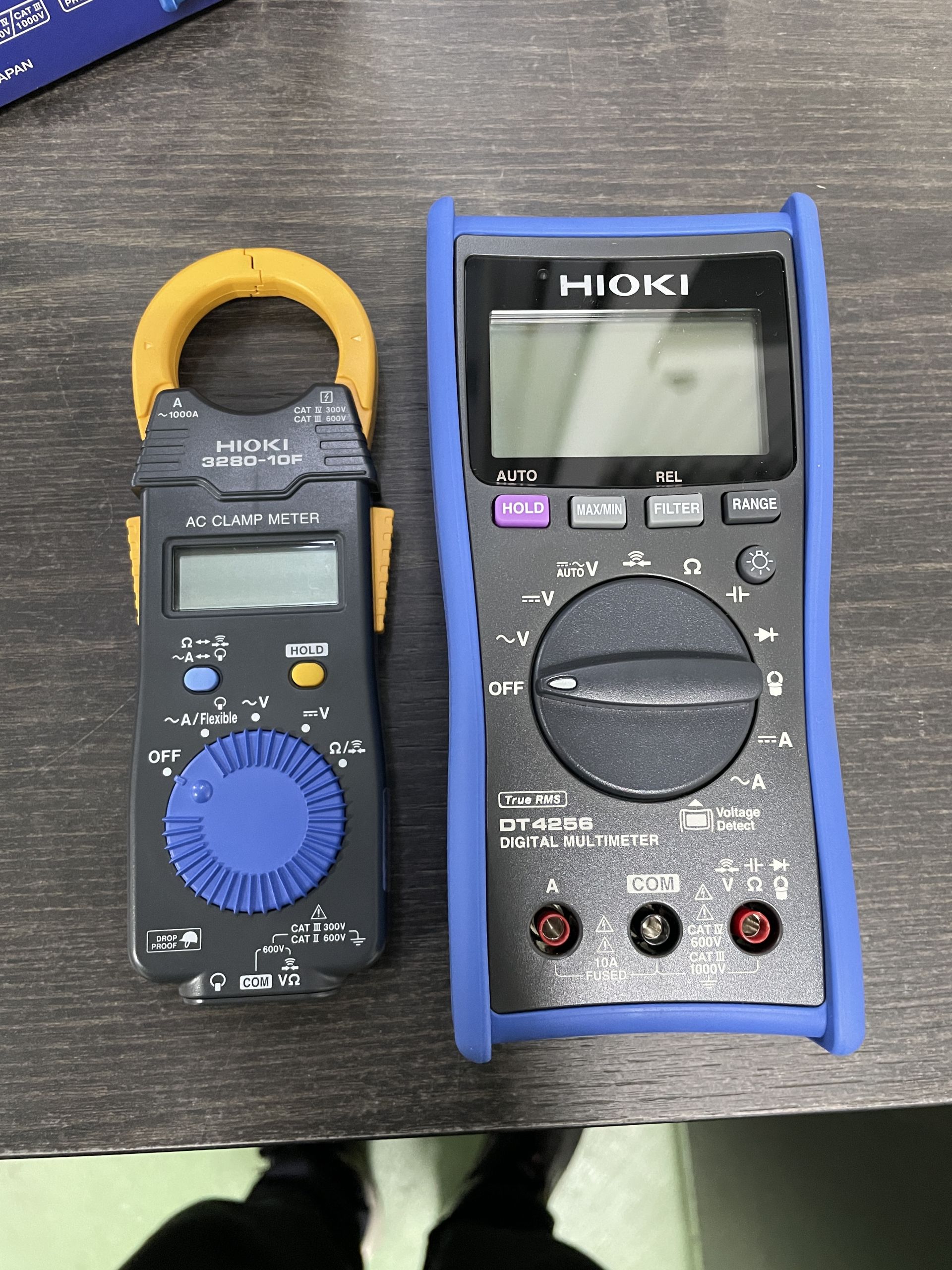
multimeter
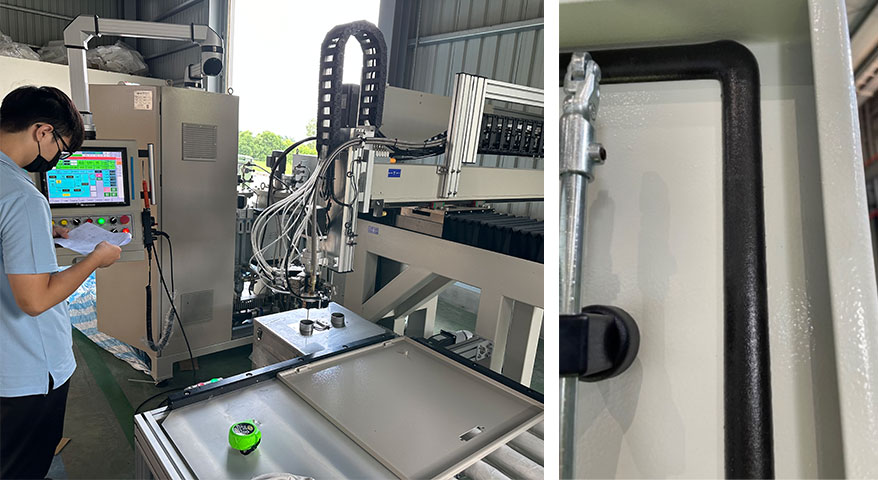
foaming machine
In the past, we typically used foam rubber strips to achieve dustproofing between the door panel and the cabinet body when manufacturing distribution panels. However, this method had a common issue: over time, the foam rubber strips tended to age, compromising their waterproofing and dustproofing effectiveness. To further enhance the quality of our products, we made a proactive investment by purchasing a million-dollar foaming machine. This new technology utilizes direct foaming to significantly improve the waterproofing and dustproofing of Jianhua distribution panels. With the foaming machine, we can directly inject foam material into the space between the door panel and the cabinet body during the production process, forming a strong, sealed protective layer.